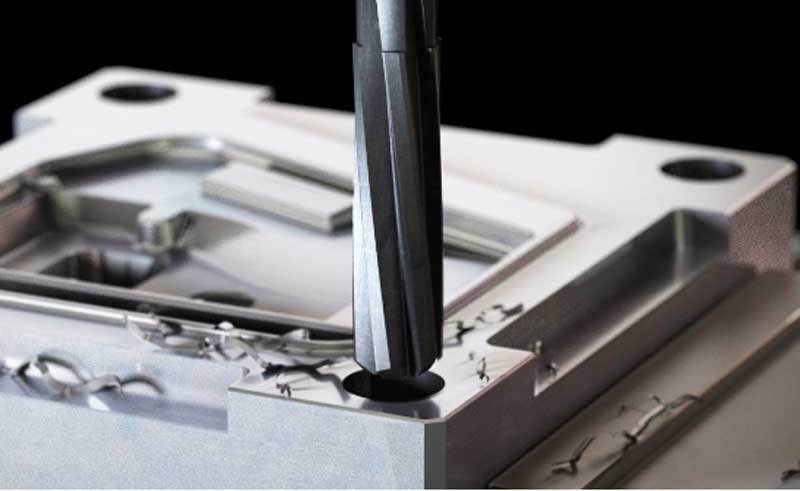
Application of Reaming
A reamer is a finishing tool used for hole processing. It is mainly used to precisely trim the inner holes that have been pre-drilled, bored or punched to improve the hole's dimensional accuracy, geometric shape accuracy (such as roundness, cylindricity) and surface finish. It is one of the core tools for high-precision hole processing in mechanical manufacturing.
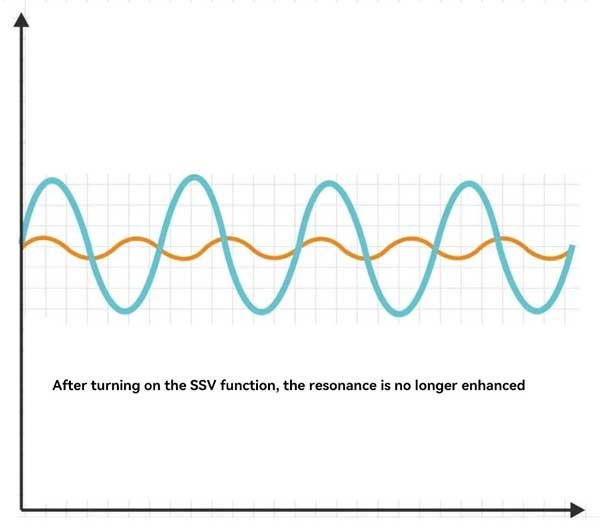
Spindle speed floating function SSV
In the application of CNC lathes, the spindle speed variation (SSV) function effectively breaks the resonance frequency during the processing, reduces chattering, and improves processing stability by introducing small periodic fluctuations around the spindle speed. Based on the set speed, the system makes the spindle speed fluctuate periodically within a small range instead of maintaining a constant speed.

How to Select Appropriate Machining Parameters for Deep Hole Drilling
Deep hole drilling refers to a drilling technique where the depth-to-diameter ratio of the hole exceeds 10:1. This process places higher demands on tool structure, chip evacuation capability, coolant and lubrication systems, as well as machine rigidity. To ensure smooth chip removal and thermal stability during prolonged drilling operations, deep hole drilling commonly utilizes a high-pressure internal coolant system, which provides effective cooling and chip evacuation at the cutting zone.

G72 radial roughing dynamic machining
G72 is a rough turning cycle command in CNC lathes, mainly used to automatically complete rough machining of external circles or end faces. Different from programming by cut, G72 can generate multiple tool paths at one time by setting cutting areas and parameters, realizing intelligent machining of "automatic layering and automatic feed".
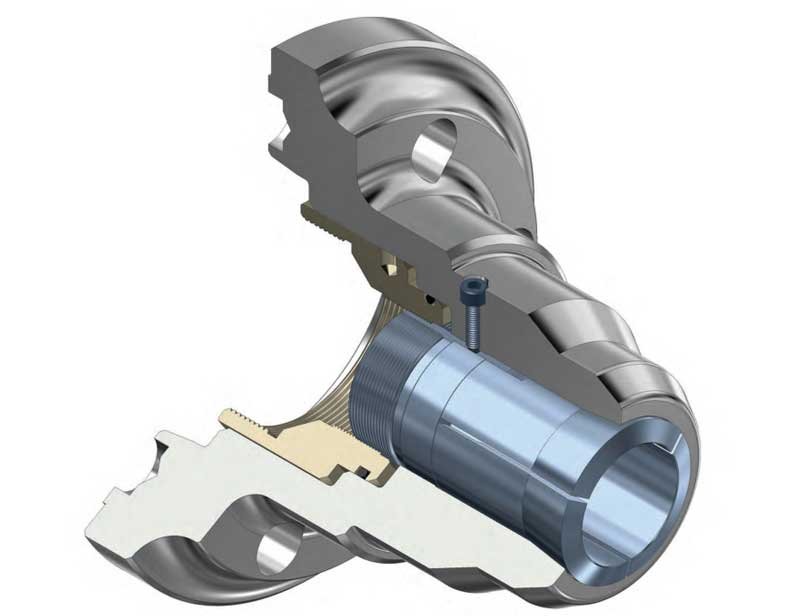
What is 5C and 16C collet?
5C and 16C are two classic American standard collet system models, designed by Hardinge Inc. in the United States and widely used in various precision turning equipment worldwide. They are precision fixtures used to hold cylindrical workpieces, relying on elastic deformation to generate clamping force, featuring high accuracy, stable clamping, and suitability for high-speed machining.
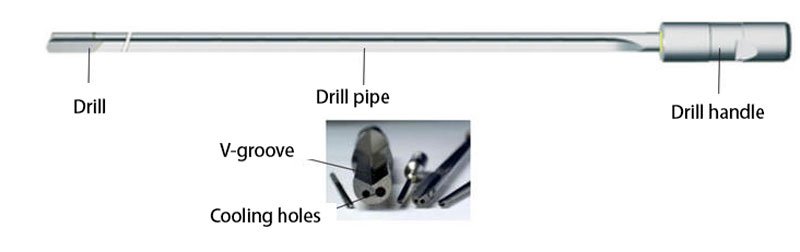
What is a gun drill
Gun drill is a special tool for small diameter deep hole processing, usually used for drilling holes with a diameter of 1mm-30mm and a depth-to-diameter ratio of up to 100:1 or more. Gun drill adopts a single-edge design, coolant enters through the center hole of the drill bit, and chips are discharged along the outer groove of the drill body, ensuring high-precision and efficient processing.
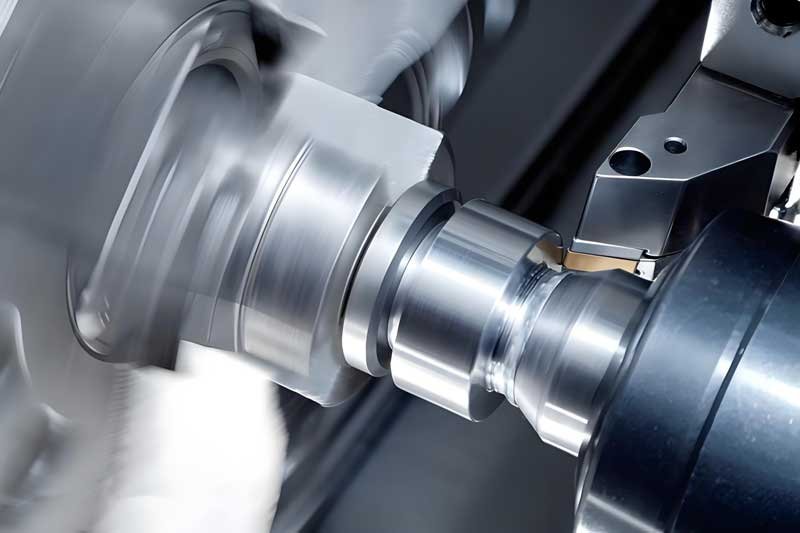
Causes and countermeasures of machining vibration problems
In CNC milling, vibration may occur due to the limitations of cutting tools, tool holders, machine tools, workpieces or fixtures, which will have a certain adverse effect on machining accuracy, surface quality and machining efficiency. To reduce cutting vibration, relevant factors need to be considered. The following is a comprehensive summary for your reference .
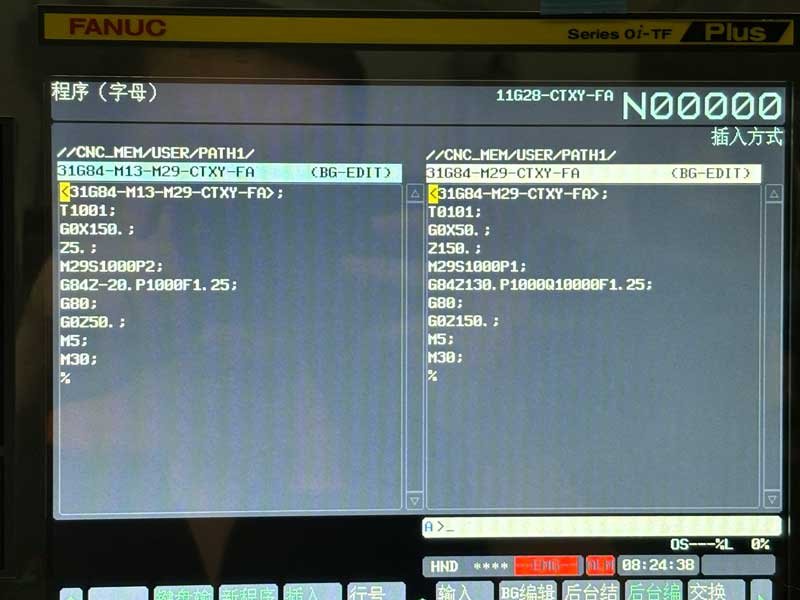
Differences in programming between Fanuc and GSK
Both systems support ISO standard G-codes such as G01, G02, G03, etc. The basic programming logic is similar.
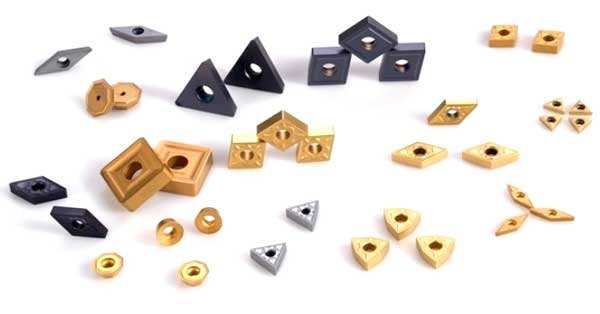
CNC Tool Classification
In modern manufacturing, CNC lathes have become indispensable processing equipment. As the "teeth" of CNC lathes, tools play a crucial role in determining machining efficiency and product quality. This article will help you understand the classification and characteristics of CNC lathe tools, enabling you to select the most suitable tools for your production needs.
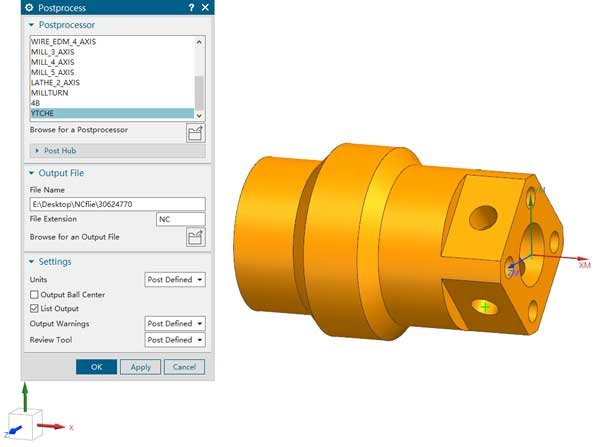
NX post-processing import and machine head connection settings
NX post-processing import and machine head connection settings
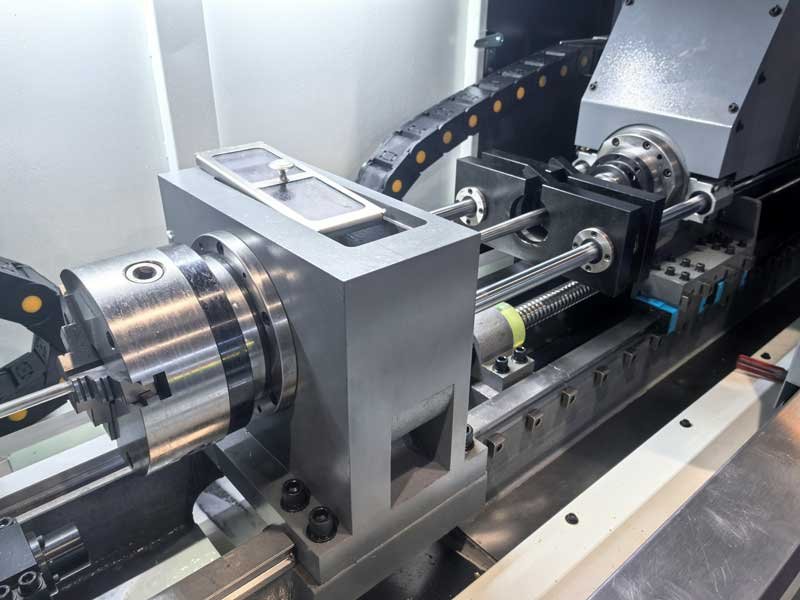
What is Deep Hole Drilling?
A deep hole is defined by its depth-to-diameter ratio (D:d), and typically holes greater than 10:1 are considered deep holes. Deep hole machining is widely used in manufacturing industries such as aerospace, automotive, mold, and energy.
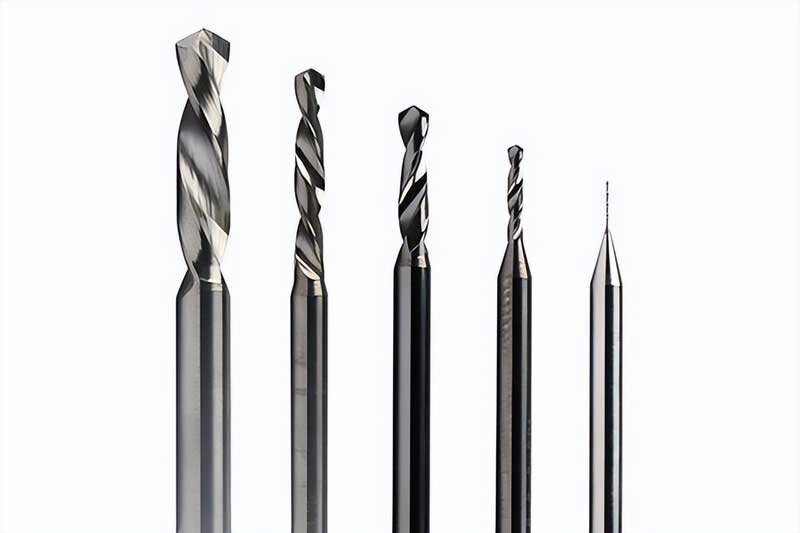
The influence of drill bit geometry on drilling
As the most commonly used cutting tool in the machining process, the drill bit's geometry directly affects the drilling efficiency, hole diameter accuracy, surface roughness, and the durability and life of the drill bit. In the drill bit geometry design, the top angle, helix angle, core thickness, chisel edge shape, edge modification, and surface coating are key parameters.
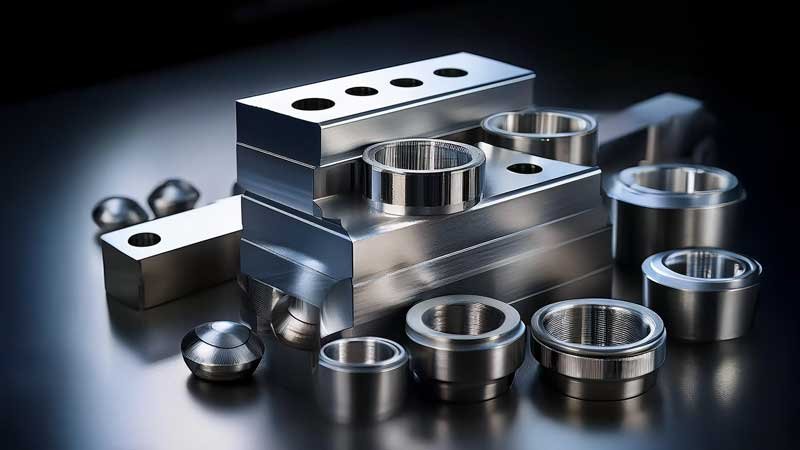
Nickel Alloy Machining Methods
Nickel alloy is a kind of metal material with nickel (Ni) as the main component and other metal elements (such as chromium, iron, molybdenum, copper, aluminum, titanium, etc.) added to improve specific properties. Due to its excellent corrosion resistance, high temperature strength and oxidation resistance, nickel alloy is widely used in aerospace, nuclear energy, marine engineering, petrochemical, medical equipment and other fields.
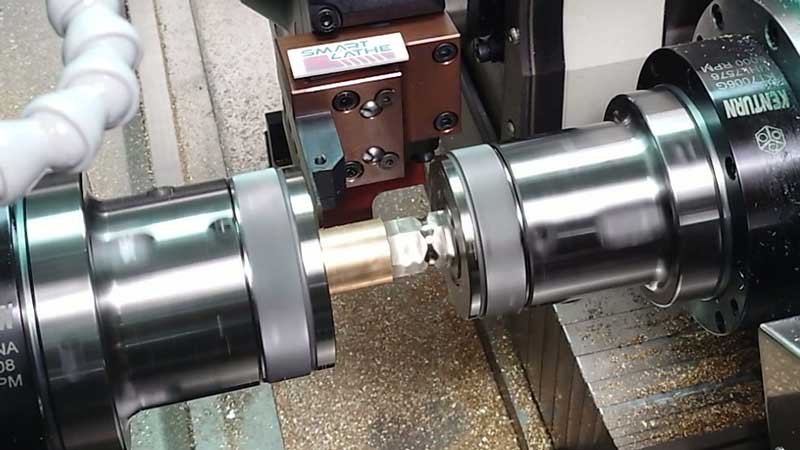
How to use a double-spindle lathe for polygonal butt jointing?
In modern precision machining, dual-spindle machines have become the industry focus due to their unique design and efficient machining capabilities. Multi-polygon alignment, as an emerging machining technique, demonstrates exceptional processing efficiency and product quality with the support of dual-spindle machines. This article will explore the technical features of dual-spindle multi-polygon alignment solutions and their advantages in practical applications.
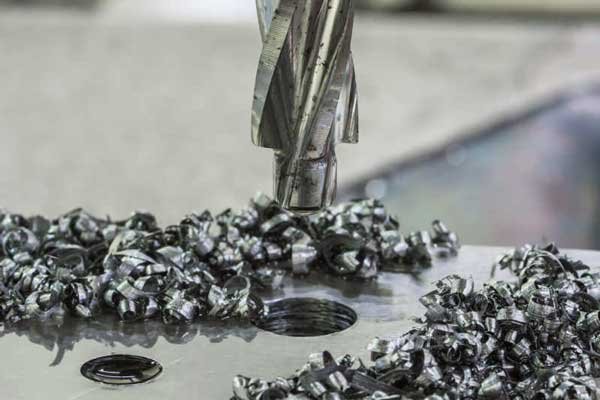
What is countersinking
Countersinking is a metal processing method that refers to processing cylindrical countersunk holes, conical countersunk holes, and boss end faces on processed holes.
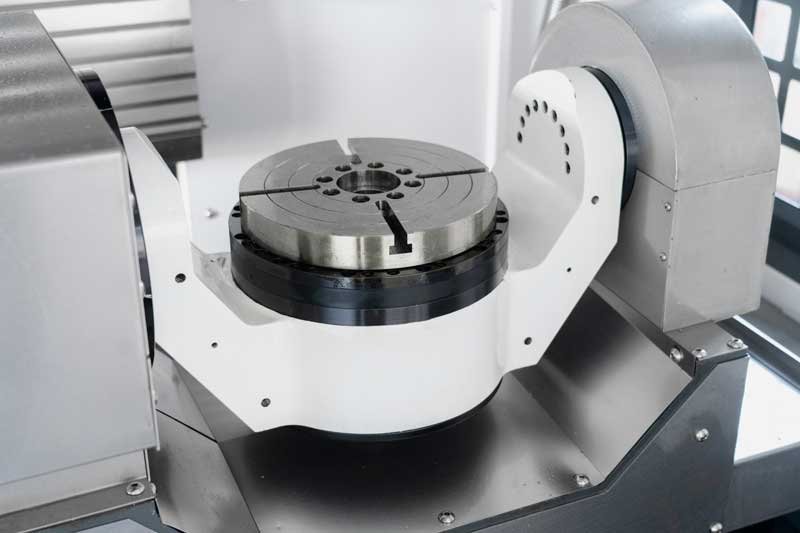
Cradle type five-axis Vertical Machining Center
The cradle-type 5-axis machining center is an important branch of the five-axis linkage machine tool. Its core feature is that the worktable adopts a "cradle" structure to realize the two-axis rotation and tilt of the workpiece, thereby forming a five-axis linkage processing method with the spindle. The five-axis machining center is a high-precision and high-efficiency CNC machine tool equipment that can control five axes for processing at the same time, usually including three linear axes (X, Y, Z axes) and two rotation axes (A, B or C axes).
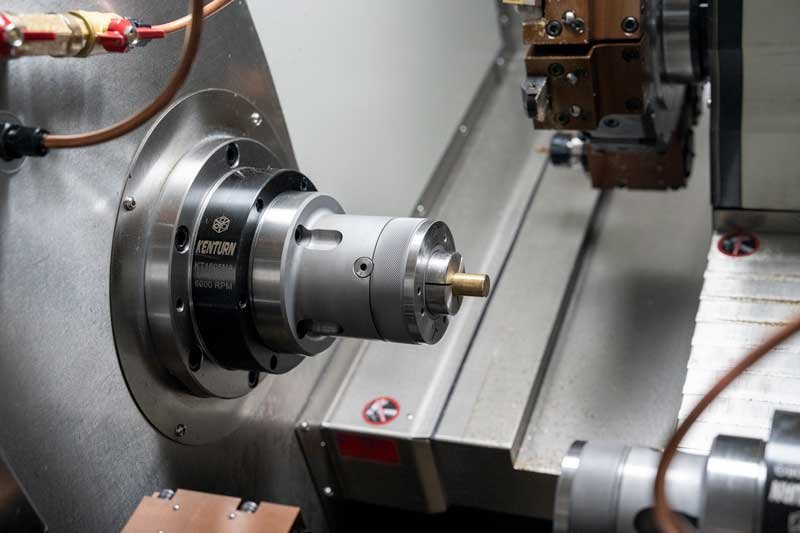
What is a push-type chuck?
A push-type chuck is a workpiece holding device commonly used in turning operations. Known for its efficient and precise clamping, it is widely employed in various CNC machine tools, especially in scenarios requiring high repeat positioning accuracy and stable clamping force.
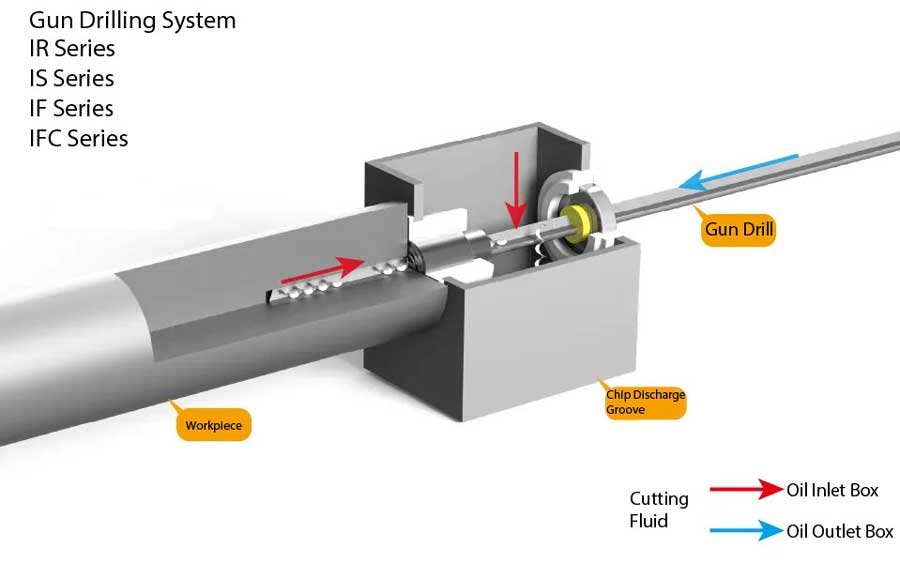
Common Types of CNC Horizontal Deep Hole Drilling
CNC horizontal deep hole drilling is a machining technology used for processing holes with large depths. It is widely applied in industries such as energy machinery, aerospace, hydraulic equipment, and petrochemicals. The machine features a horizontal spindle arrangement, with the workpiece fixed to the bed, while the drilling tool operates with high rigidity and precision. Horizontal deep hole drilling offers good machining stability and efficient chip removal, making it especially suitable for deep hole processing in long workpieces. Common types of CNC horizontal deep hole drilling include: gun drilling, BTA drilling, deep hole rolling, and electrical discharge machining (EDM).
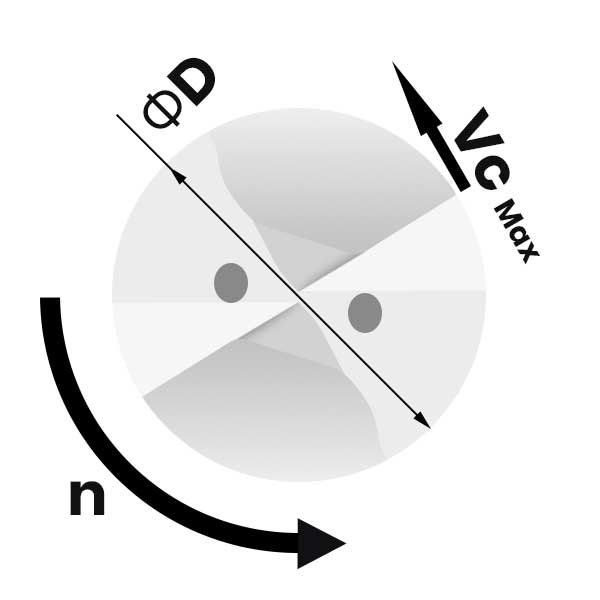
Calculation of drilling parameters
Cutting speed is the relative linear speed between the cutting edge and the workpiece. At every point, the cutting speed is the product of the drill's rotational speed (spindle speed) and the circumference. At the center of the drill, the cutting speed is always zero, and it gradually increases as you move away from the center. Therefore, in drilling, the term "cutting speed" refers to the maximum cutting speed occurring at the drill's outer diameter. On the surface of the drill, the cutting speed varies according to the distance from the center.
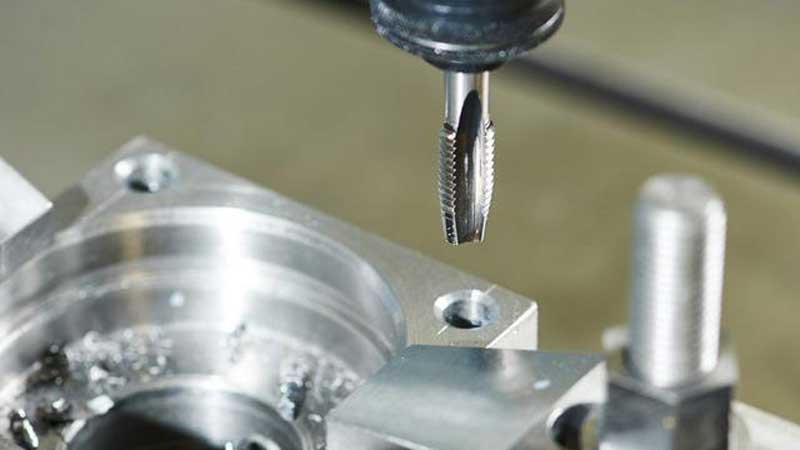
How do you do blind hole tapping?
Unlike through holes, blind holes do not pass through the workpiece. They have a bottom, which is why blind holes are often referred to as guide holes. The bottom of the hole is also a potential issue for blind hole threads, which does not occur with through holes. If not handled properly, chips can accumulate in the blind hole. Additionally, the tap may collide with the bottom of the blind hole and break, or other problems may arise. Those who frequently use taps with blind holes often encounter these issues. The primary solution to this problem is to avoid misalignment and prevent the blind hole thread from becoming larger than intended.