
The selection between True Y-axis and Wedge type Y-axis on CNC lathes
In CNC lathes, different machining effects can be achieved by selecting different Y-axis transmission methods, with the Y-axis transmission structure typically adopting two different designs: True Y-axis and wedge type Y-axis. True Y-axis utilizes Y-axis linear interpolation control, while wedge type Y-axis monitors surface contour errors in real-time and compensates by fine-tuning Y-axis movement. They each have their advantages and disadvantages.
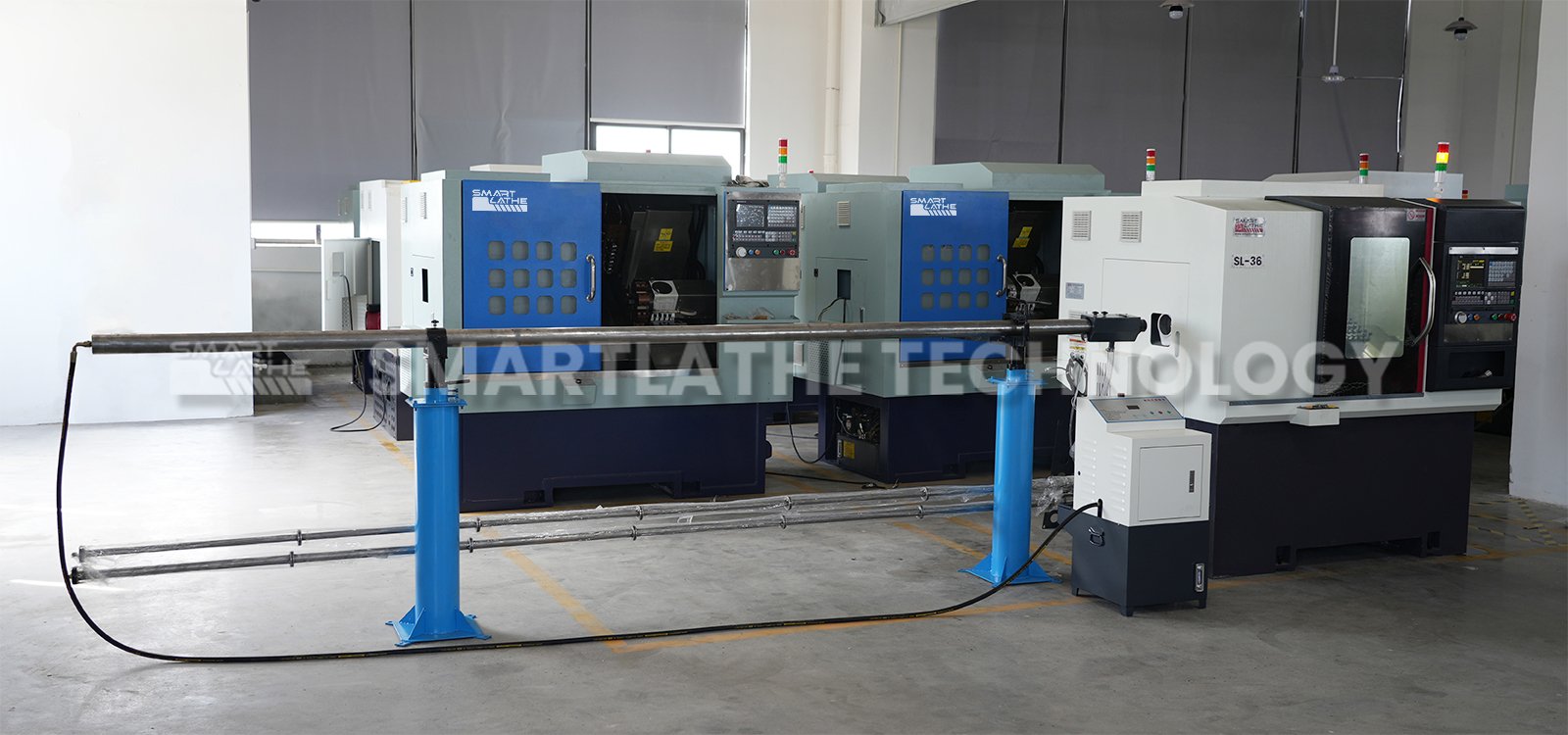
Selection of CNC Lathe Feeders
A CNC lathe feeder is an automated device used in machining processes, primarily to automatically feed materials into a CNC lathe for processing. Feeders offer advantages such as efficiency, stability, and cost savings in CNC lathe machining.
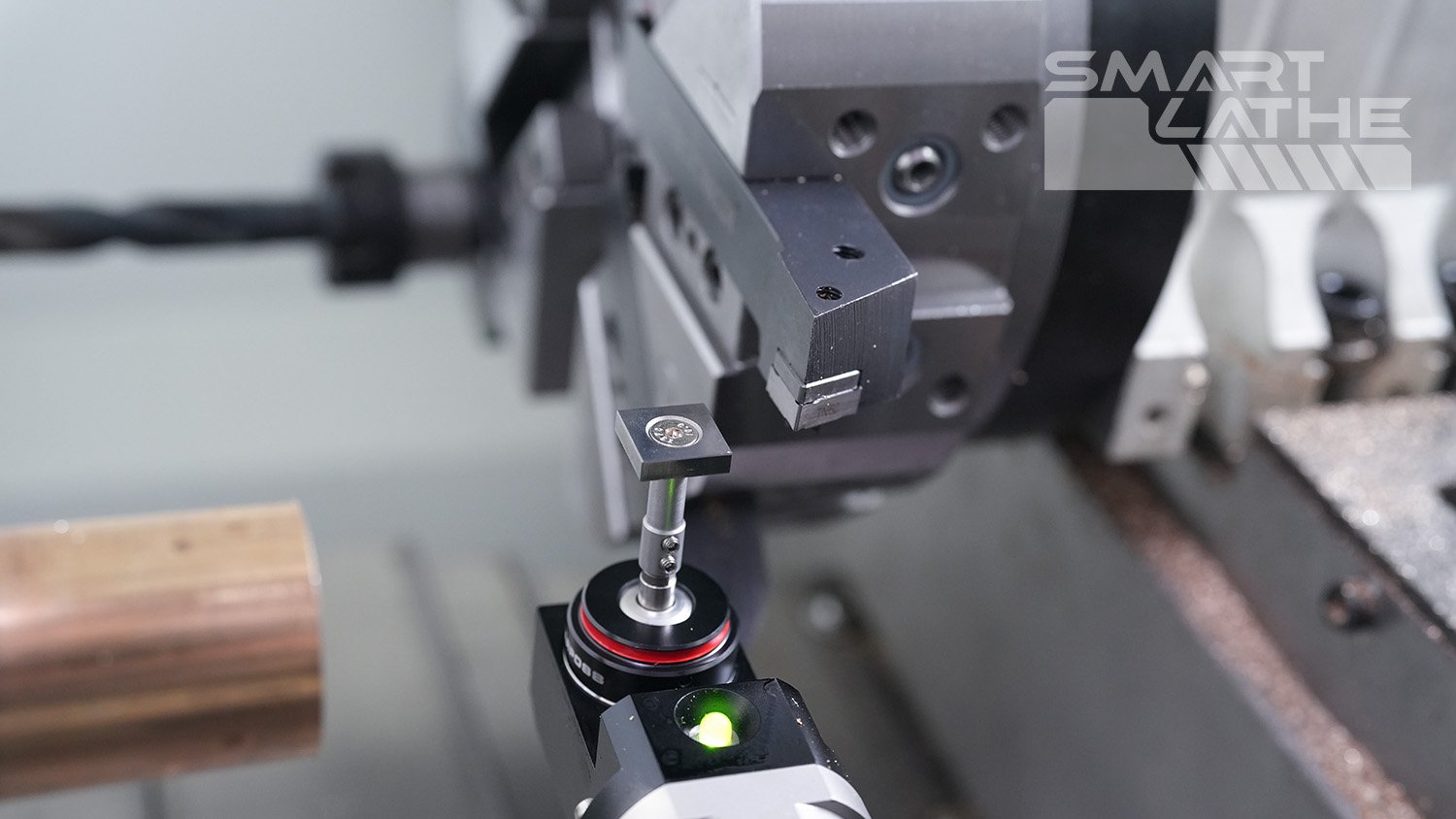
The application of tool setters on CNC lathes
On CNC lathes, the tool setter is a crucial device for ensuring the correct installation and positioning of tools, as well as monitoring and adjusting tool conditions.
Pneumatic transmission and hydraulic transmissions in CNC lathes
Pneumatic transmission utilizes gas, typically air, to transfer energy and is commonly employed for actuator driving in automation systems. Its characteristics include easy installation, low maintenance costs, and operational safety. Suitable for tasks like rapid tool changing, positioning, and clamping, it finds wide application across automation equipment, manufacturing, and industrial production lines. On the other hand, utilizes liquid, usually oil, to transfer energy, prevalent in power transmission and control within mechanical systems. Hydraulic transmission systems compress and flow liquid to achieve various actuator movements and controls, such as hydraulic cylinders and motors. Its characteristics include high load-carrying capacity, precise control, and high reliability. Hydraulic transmission is extensively used in heavy machinery, engineering equipment, automotive braking systems, providing effective power support across various industrial applications.

CNC lathe chuck types
CNC lathe is a type of high-precision, high-efficiency automated machining equipment. There are various types of chucks used on its spindle, which can be categorized based on their clamping methods and structural characteristics. The following are types of chucks commonly used on CNC lathes
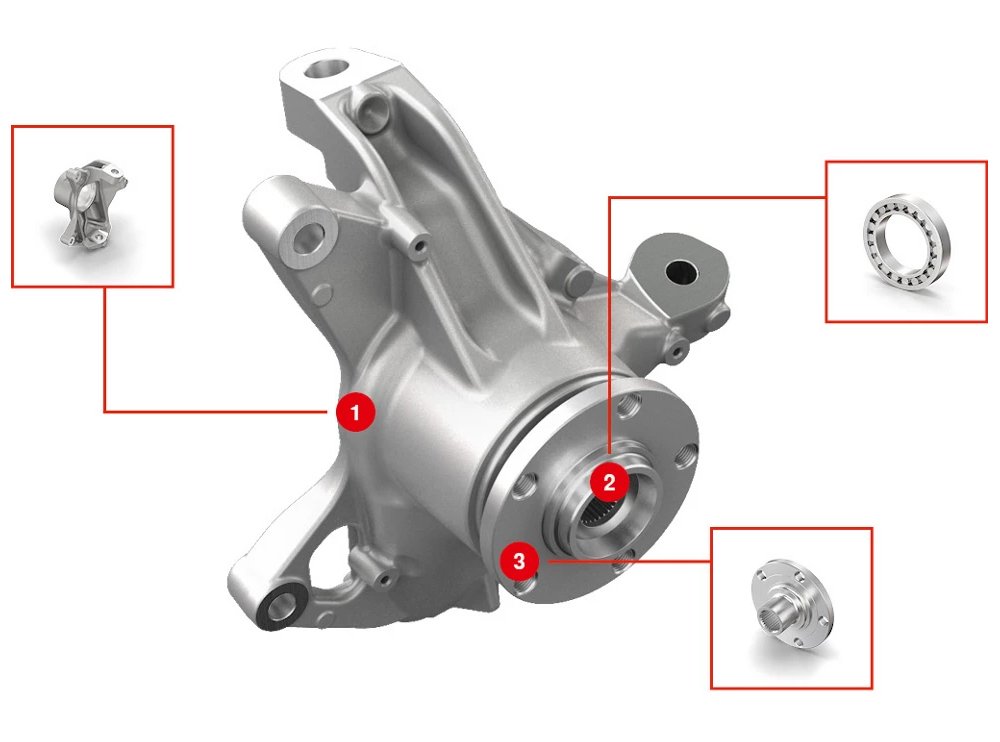
Application of CNC Lathe in the Field of New Energy Vehicles
The field of new energy vehicles is one of the key areas for the application of new energy technologies. With increasing global attention to environmental protection and climate change, the market for new energy vehicles is rapidly expanding. Electric vehicles have become the mainstream choice, with their sales increasing year by year. Major automobile manufacturers are introducing electric models, accelerating the development of the new energy vehicle industry chain. At the same time, technological innovations in electric vehicles, such as battery technology, charging technology, and intelligent driving technology, have made significant breakthroughs. Governments also encourage and promote the development of new energy vehicles through policy support and subsidies. In the future, with advancements in technology and reductions in costs, the field of new energy vehicles will have even broader development prospects, making greater contributions to reducing exhaust emissions and improving energy efficiency.
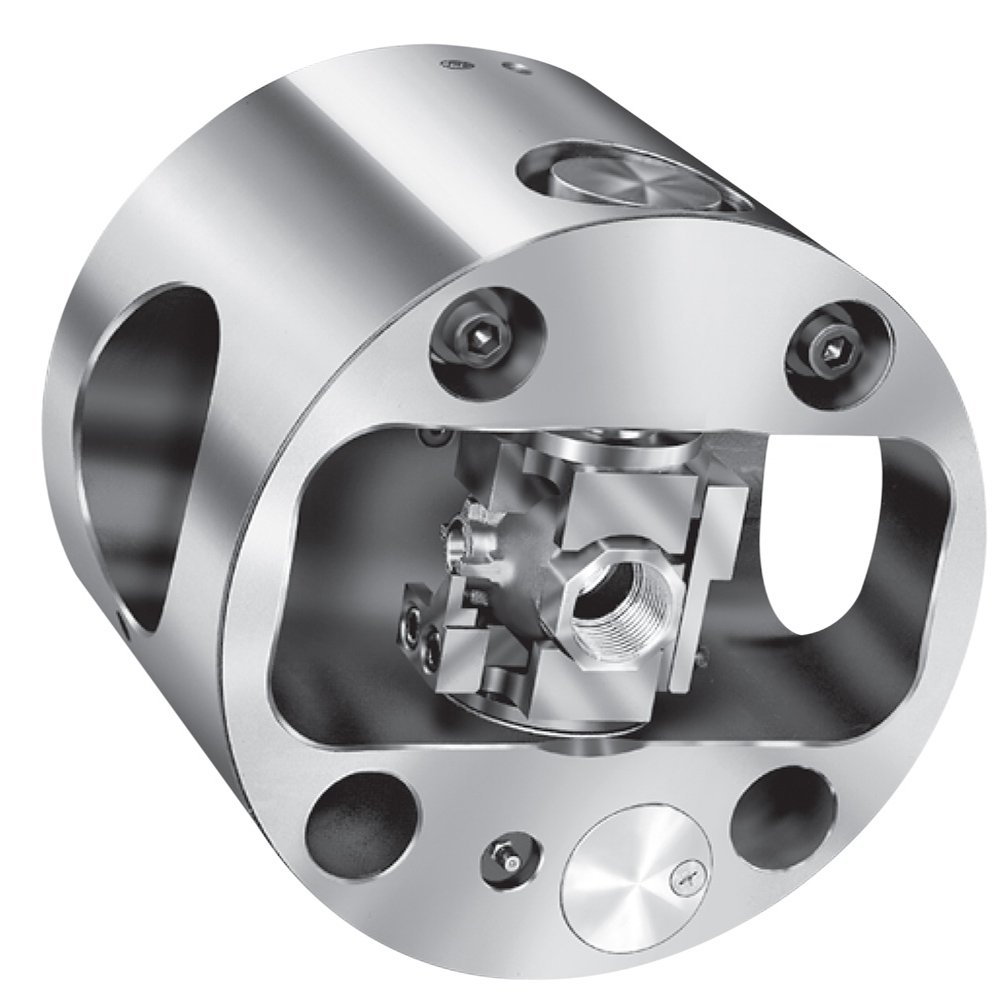
What is Indexing Chuck
The indexing chuck plays a crucial role in CNC lathe machining, serving as one of the key tools for achieving precise workpiece machining and efficient production.
In recognition of the machining advantages of indexing chucks, SMART LATHE has taken proactive steps to offer sales and customization services for indexing chucks, keeping pace with the times. Moreover, these indexing chucks are matched according to the CNC lathes available at SMART LATHE.
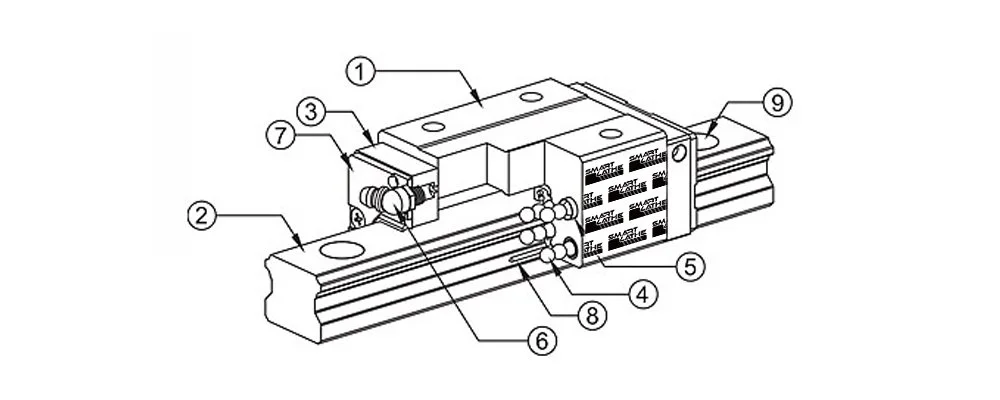
Types of Guideways in CNC Lathes
CNC lathes, as crucial equipment in modern manufacturing, often directly affect product quality and production efficiency. Guideways, as one of the core components of CNC lathes, play a vital role in the motion system of the machine. This article will explore common types of guideways in CNC lathes, with a focus on comparing linear guideways and V-type guideways, and analyzing their respective advantages and disadvantages.

The processing technique of controlling roughness by controlling cutting parameters for materials of different hardness
In metal turning processes, the surface roughness of metal is influenced by numerous variables. Today, we're discussing how surface roughness is affected by different cutting parameters for metals of varying hardness when other variables remain constant.

What is turn-milling combination?
The names of various CNC lathes steadily get more cryptic as the variety of lathe types grows. We will then go over what a CNC turn-mill combination is. Prior to comprehending the CNC turn-mill combination, it is important to first comprehend the CNC lathe and CNC milling machine independently and determine their prior differences.

Turning vs Milling: What’s the Difference?
To put it simply: lathes are round, milling machines are flat. In lathe operations, the cutter is stationary while the workpiece rotates. The workpiece does not revolve during milling machine processing; instead, the tool rotates.

What is ER collet with CNC lathe
The subtype of chuck known as a collet is a cylindrical sleeve. With a pointed outer surface and a tube-shaped inner surface, the sleeve is used to create a collar around a tool or gadget. Collets have a conical outer surface that often provides a strong gripping force on the thing they are grasping when tightened.

What’s the information that we can get from the drawings?
As the professional CNC lathe supplier, we always to recommend the suitable CNC lathe model with related configuration base on customized drawings of jobs.

Exploring the Versatility of Power Turret
The power turret, a prevalent feature in CNC machine tools, combines turning and milling capabilities. It boasts multiple mounting planes and slots along its circumference for attaching various tool holders, including turning, boring, 0-degree power, 90-degree power, right-angle internal retracting power, eccentric power, and dual-spindle output tool holders.

Comparing Three-Phase Induction Motors and Servo Motors, Which Is the Better Choice?
In modern industrial manufacturing, motors are crucial for driving equipment, with three-phase induction motors and servo motors being common choices. They differ significantly in performance, application, and benefits. This article will compare the two types, aiding your understanding of their pros and cons in CNC lathe applications.
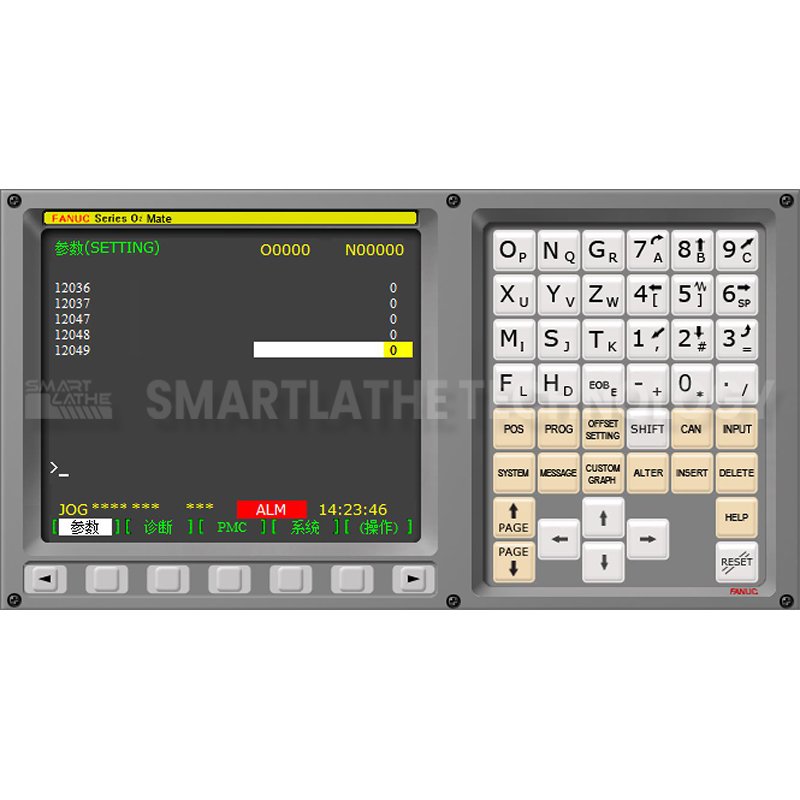
Analysis of Conversational Programming and Graphics Support Functions of Multiple CNC Lathe Operating Systems
In the increasingly competitive landscape of manufacturing, the efficiency and accuracy of CNC programming are crucial for production processes. To meet this demand, several CNC system providers have introduced conversational programming and graphical support features to enhance users' programming experience and production efficiency. This article provides an overview of seven major CNC system: Fanuc, Siemens, SYNTEC, Beijing-Fanch, GSK, KND, and HNC. So that you can understand the characteristics of different CNC systems and choose the system that is suitable for your CNC lathe.
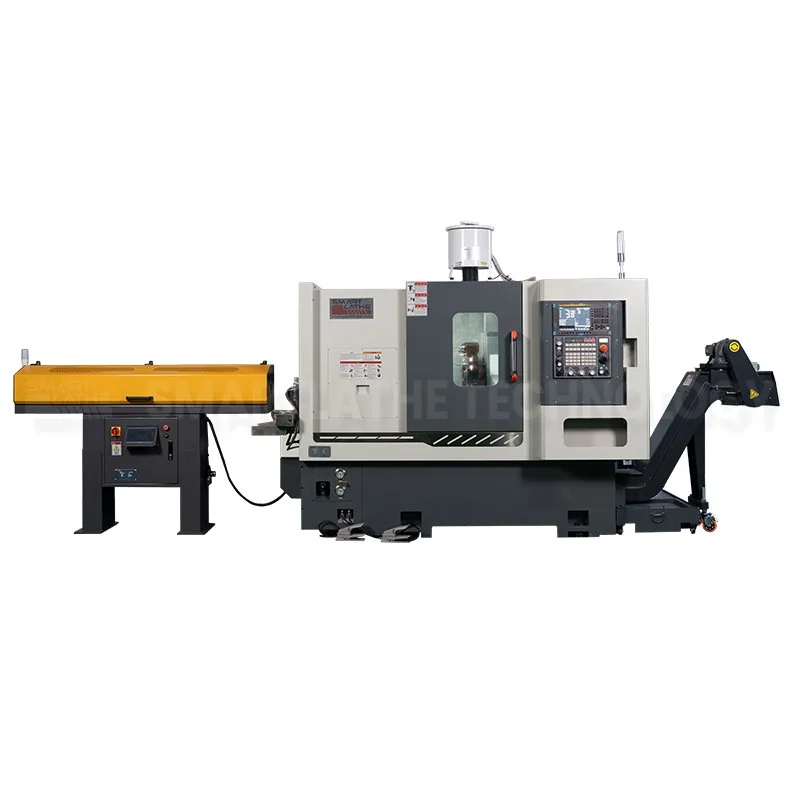
A Comprehensive Chronicle of the ST-46YTC CNC Lathe Project – From Client Vision to Shipment Perfection
Client’s requirement: The client provides detailed requirements for the workpiece and machine.
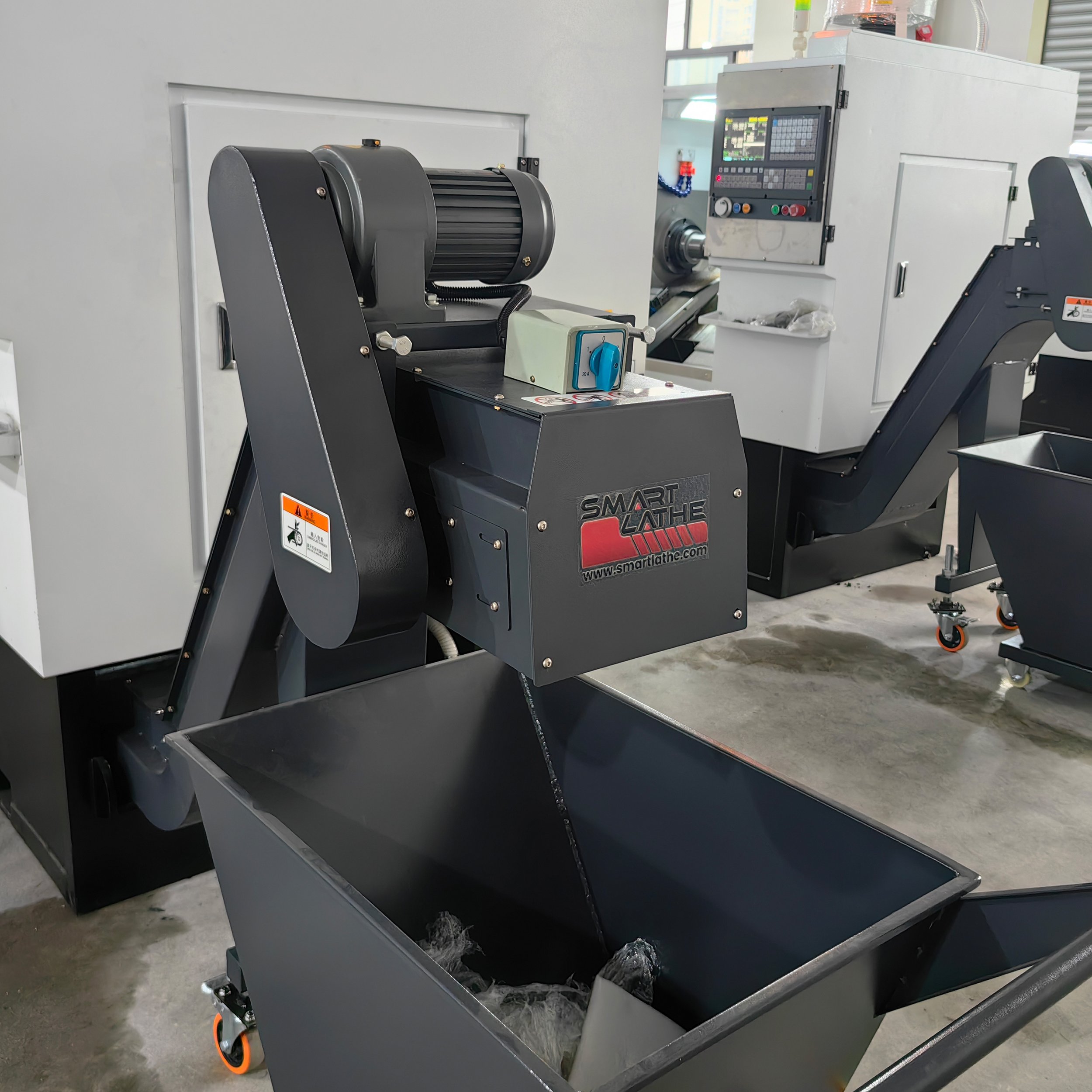
Enhancing CNC Lathe Efficiency with Chip Conveyor
A chip conveyor is a machine primarily utilized to gather various metal and non-metal waste produced by machinery and transfer it to a collection vehicle. It contributes significantly to maintaining a clean work environment, reducing manual labor, and preventing chip interference with machining operations. And it can easily collect metal waste.
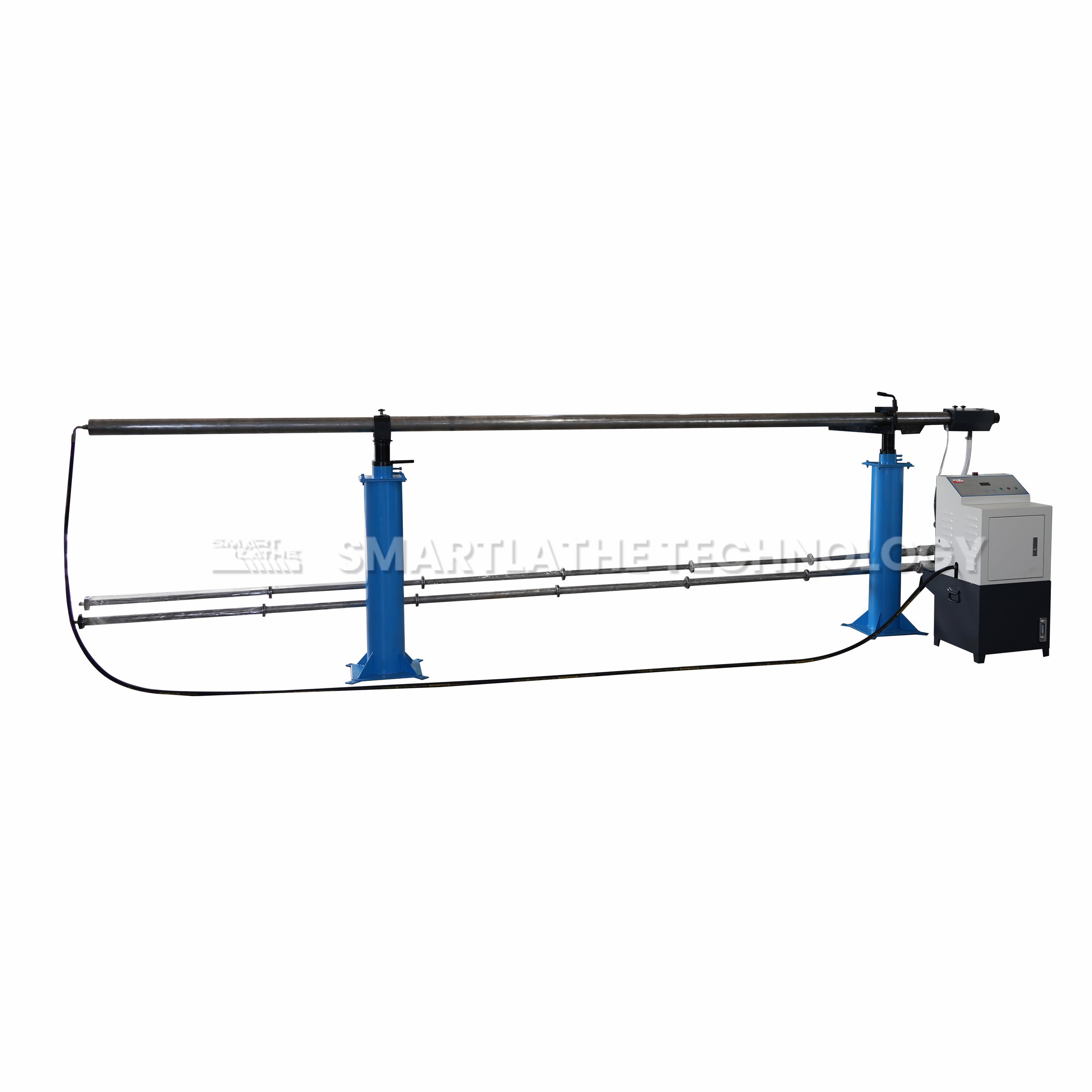
Choice of Automatic Bar Feeder for CNC Lathes, Oil Bath Bar Feeder, or Servo Bar Feeder?
CNC lathe automatic feeder refers to a feeding machine that cooperates with a CNC lathe that can continuously process materials to achieve automatic feeding, thereby improving the processing efficiency and automation of the equipment.
Oil bath bar feeders and servo bar feeders are common automatic feeding equipment, and they have different working principles and features.
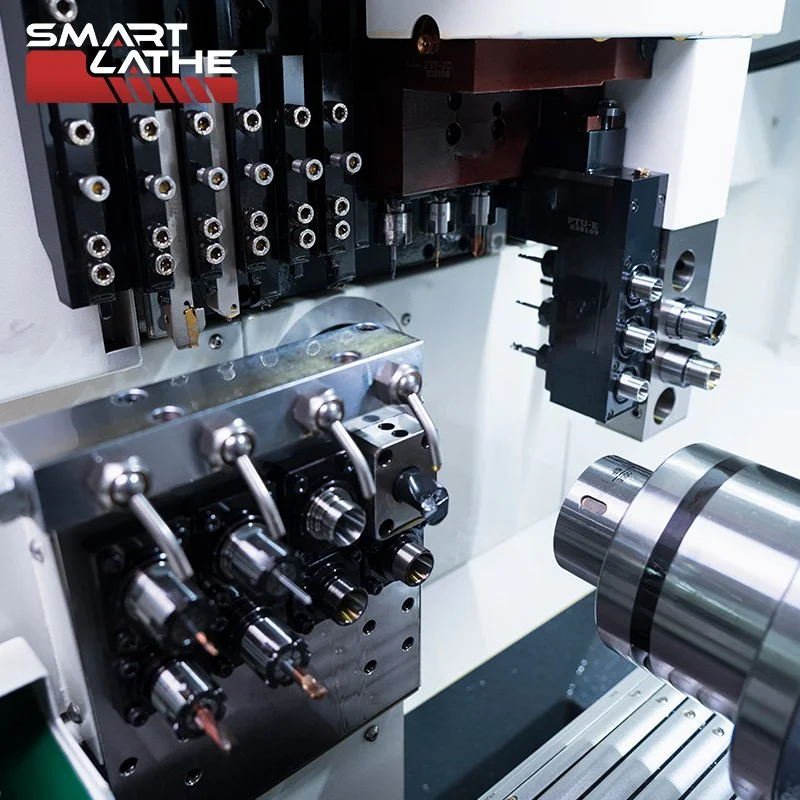
What is a Swiss Type CNC Lathe?
A Swiss-type CNC machine, also known as a Swiss-type lathe or Swiss automatic lathe, is a high-precision machine tool designed for machining small, complex parts. It has gained recognition in the manufacturing industry for its outstanding precision machining capabilities and efficiency.
The working principle of Swiss-type CNC lathe tools is guiding a long metal rod through supporting components and securely holding it in place as it enters the cutting area of the machine. Only the portion of the metal rod that requires machining moves into the cutting area, ensuring stability and accuracy.
Ordinary CNC lathe machined workpieces remain stationary and rotate rapidly, with one or both ends of it being tightly fixed. But with a Swiss-type CNC lathe, the workpiece can rotate and move back and forth on the Z-axis as the tool forms it. Swiss-type CNC lathe can do many tasks in different areas at the same time.